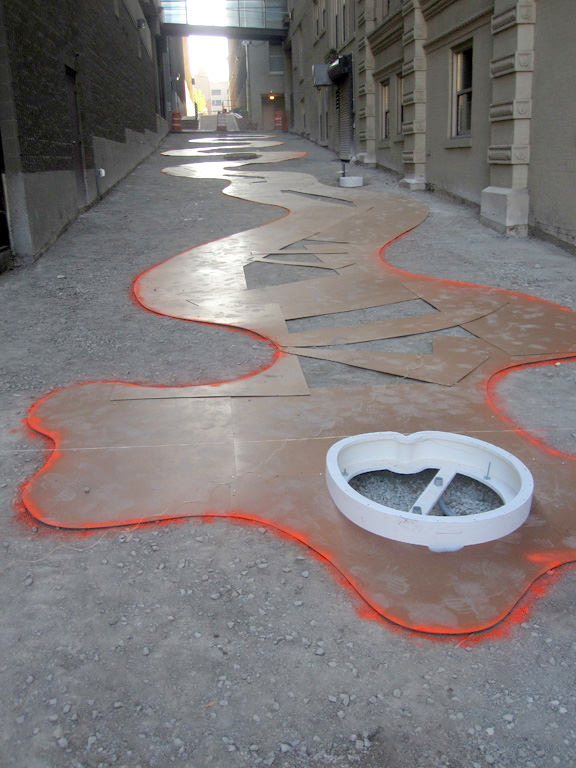
The Commons, downtown Kansas City :: 2012.
Alley from the street end, after demolition, with the stream template and whirlpool template in place. Because we wanted to maintain complex organic curves and were working within a relatively limited budget, we cut templates for the formwork using our CNC router.
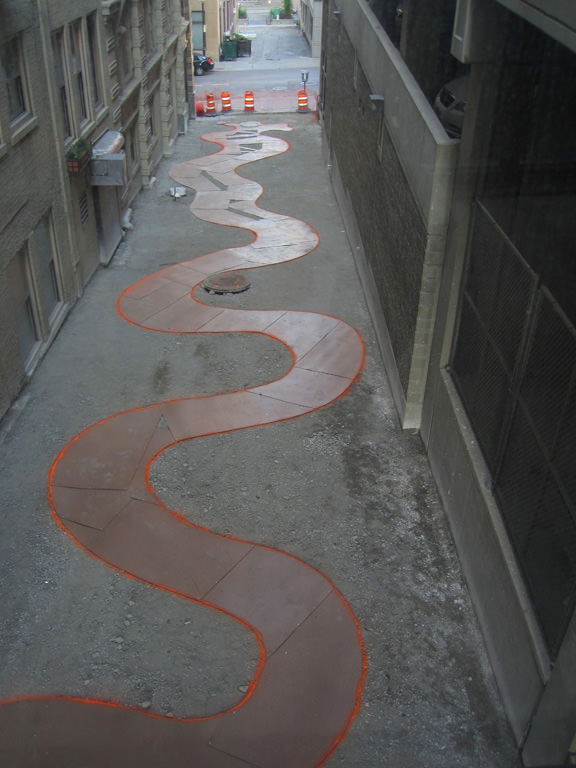
The Commons, downtown Kansas City :: 2012.
Alley from rear, slightly above, stream template in place. This method also allowed us to easily visualize the design on site prior to implementation.
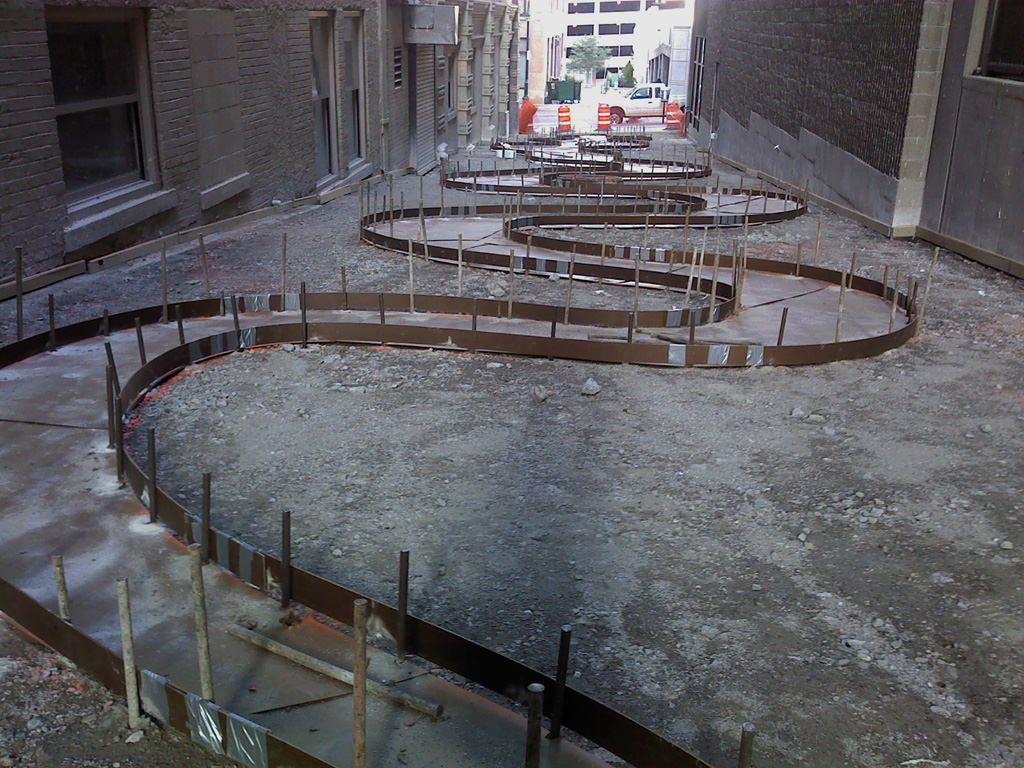
The Commons, downtown Kansas City :: 2012.
Alley from the rear, with the stream template and forms in place. The concrete crew was then able to set the forms tightly to the curves we specified. There was still some flattening that happened in small areas, but it was relatively simple to grind these after the first pour.
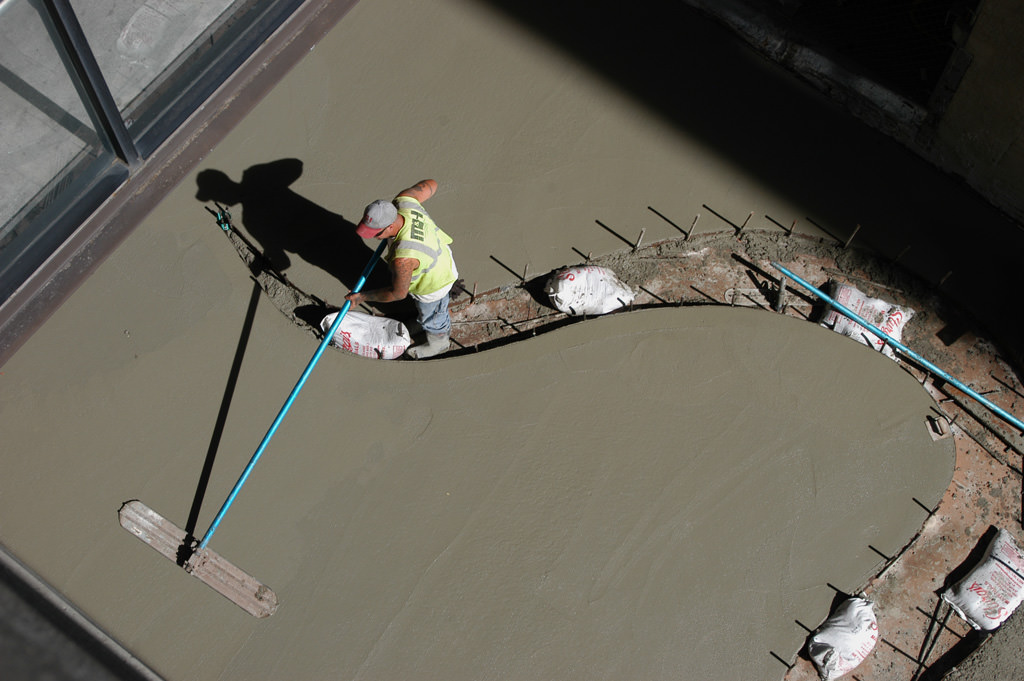
The Commons, downtown Kansas City :: 2012.
The rear end of the alley, from above, during the outside pour. The brushed grey concrete surround was poured first.
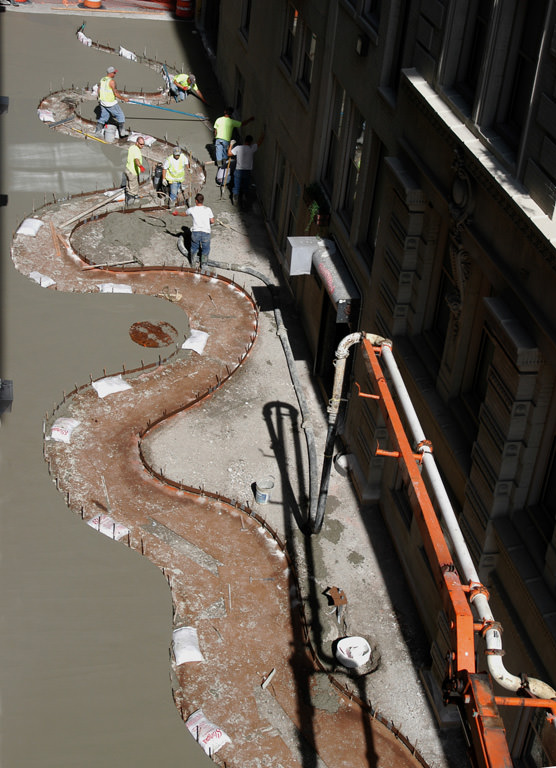
The Commons, downtown Kansas City :: 2012.
Towards the back end of the alley, from the parking structure, showing the outside pour using a concrete auger.
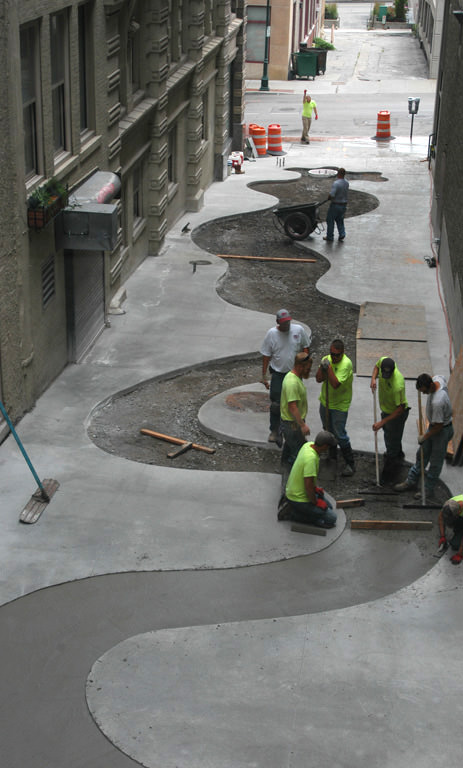
The Commons, downtown Kansas City :: 2012.
After the outside pour had hardened, the forms were removed and a shallower layer of grey concrete was poured inside the stream area.
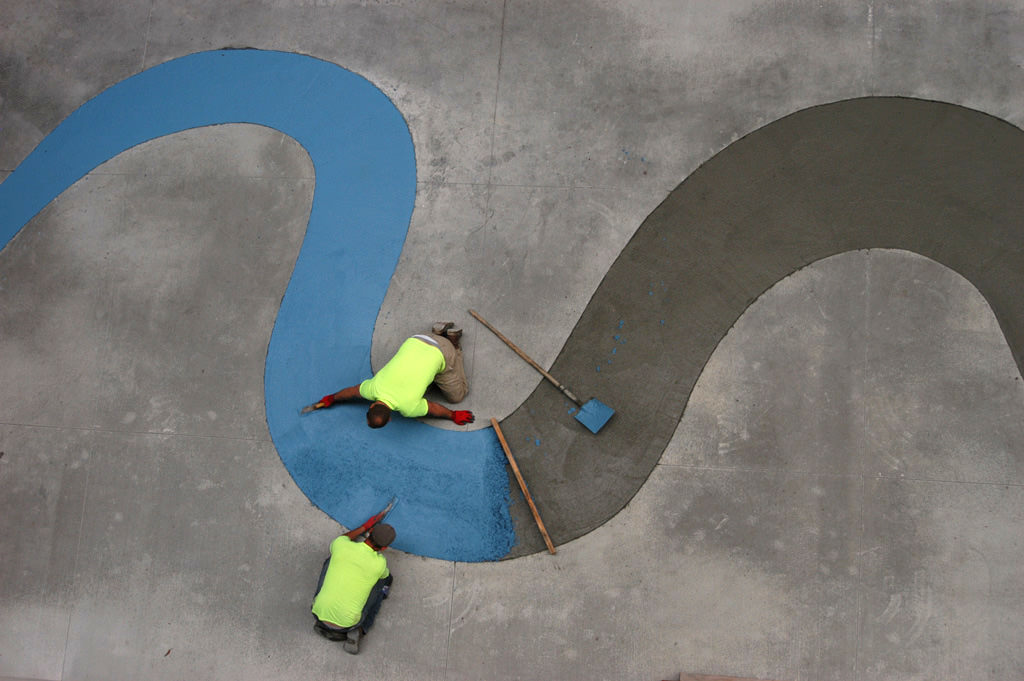
The Commons, downtown Kansas City :: 2012.
When the inner grey concrete had firmed up but not started to harden, a second thin layer of concrete was poured on top. This layer contained blue pigment and the aggregate mixture we had chosen to create a surface texture.
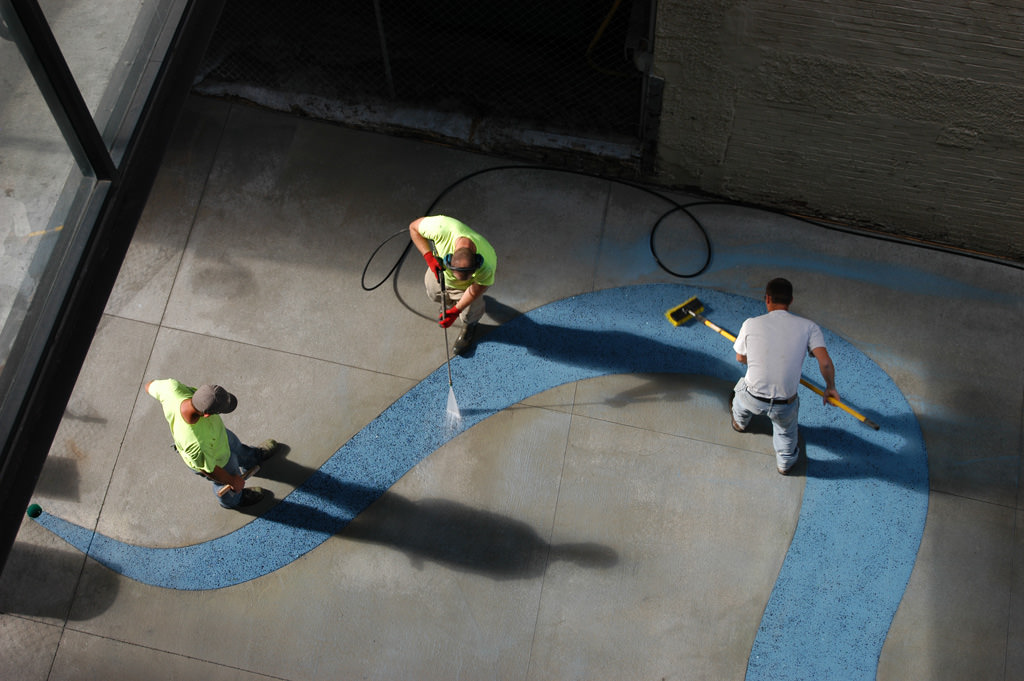
The Commons, downtown Kansas City :: 2012.
Before the material had completely hardened, the surface was pressure-washed to reveal the aggregate mix.
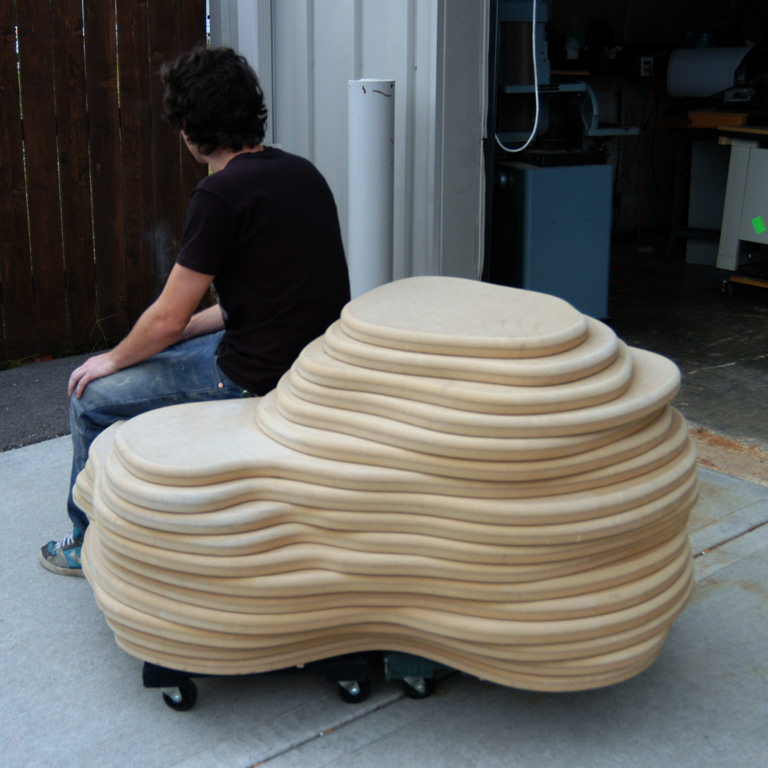
The Commons, downtown Kansas City :: 2012.
Prototype of a seating unit made out of MDF (on a dolly).
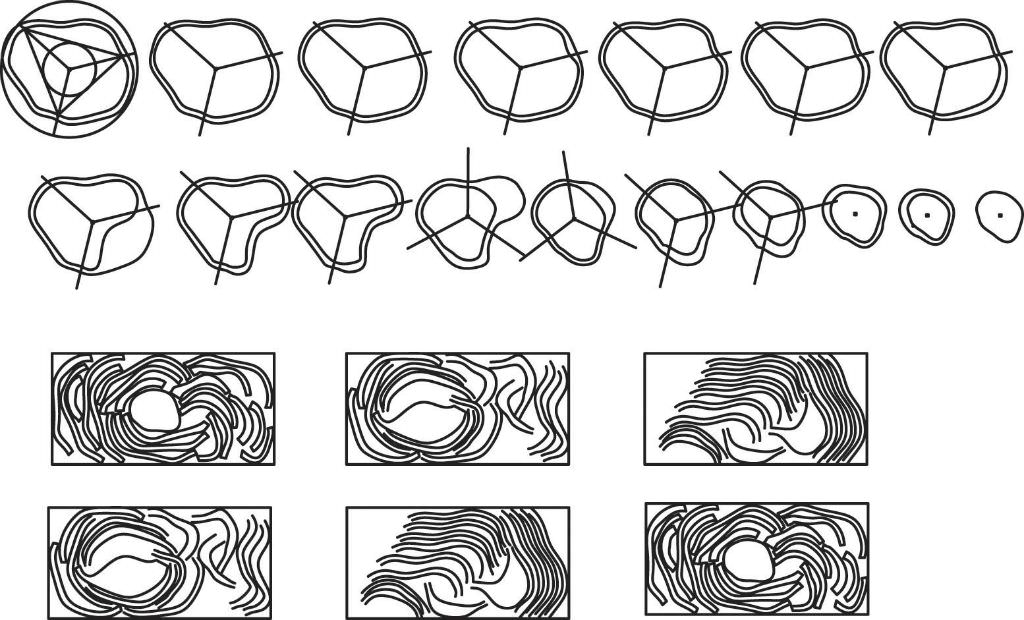
The Commons, downtown Kansas City :: 2012.
Schematic for material layout. The seating units were constructed by assembling segments of HDPE that were cut on a CNC router and then stacked in layers, to maximize the efficient use of the material.
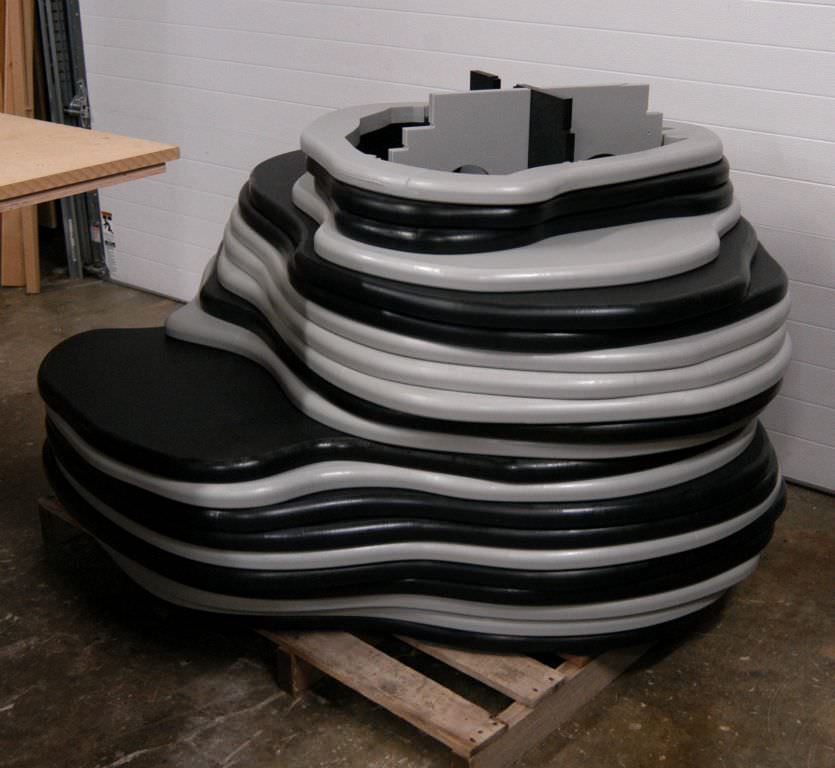
The Commons, downtown Kansas City :: 2012.
Each seating unit has a supporting internal structure and a concealed locking mechanism that allows for disassembly if required.
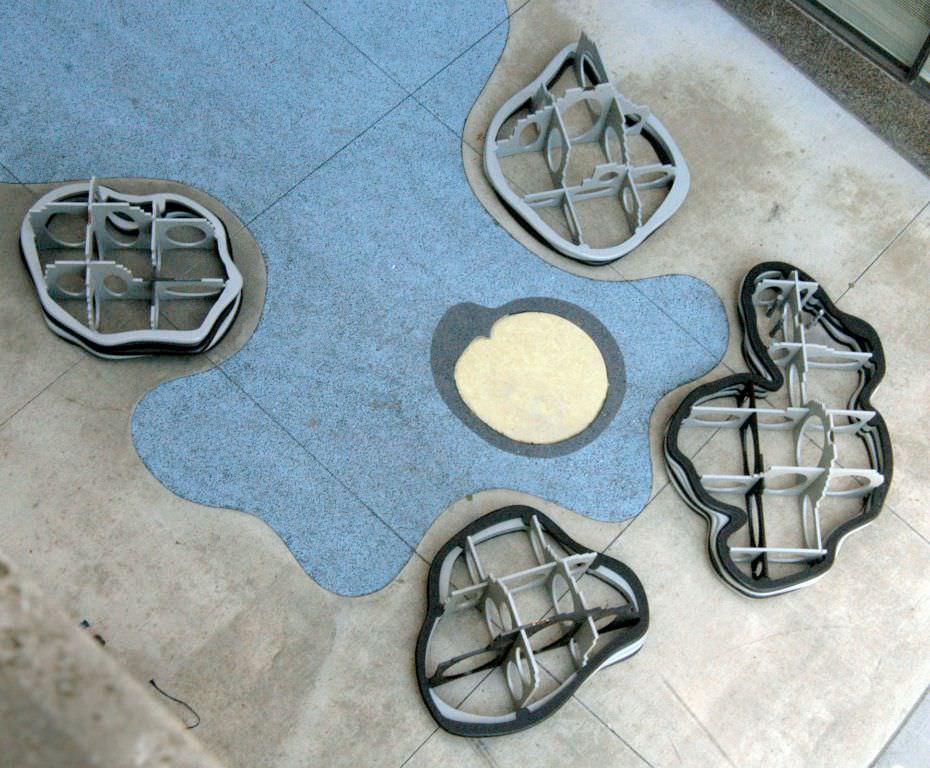
The Commons, downtown Kansas City :: 2012.
Installation of the seating units on site. The embedded lighting unit is not yet in place.
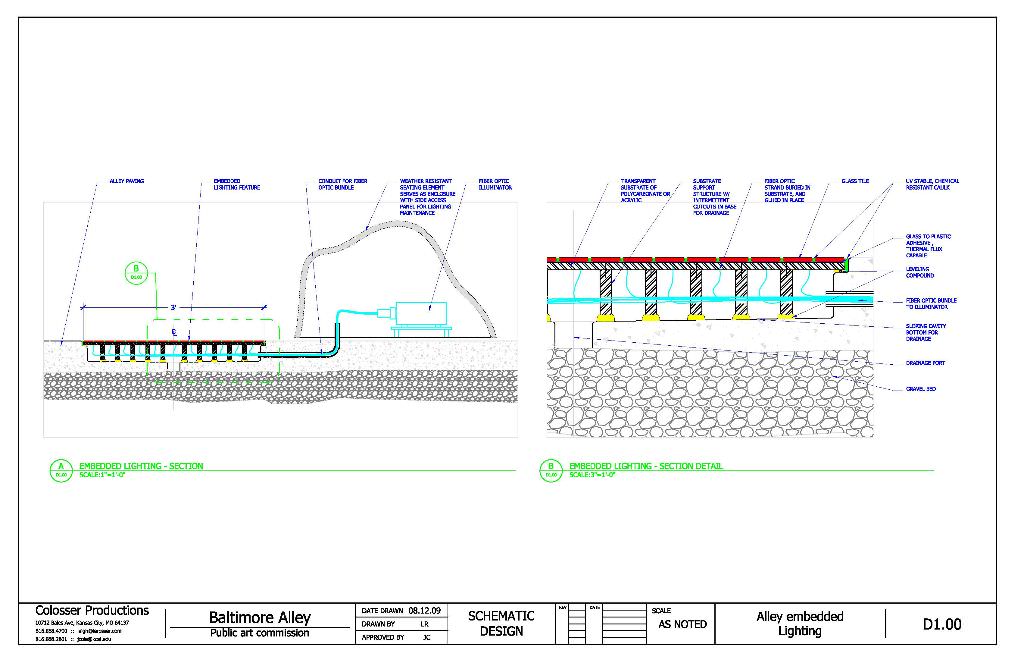
The Commons, downtown Kansas City :: 2012.
Design schematic for the embedded lighting forms. Each of the two seating areas features an illuminated glass tile that is sunk into the pavement. Light patterns are generated by high efficiency LED illuminators concealed in two of the seating units, and maintenance-free fiber-optic transmission from there to the embedded glass tiles.
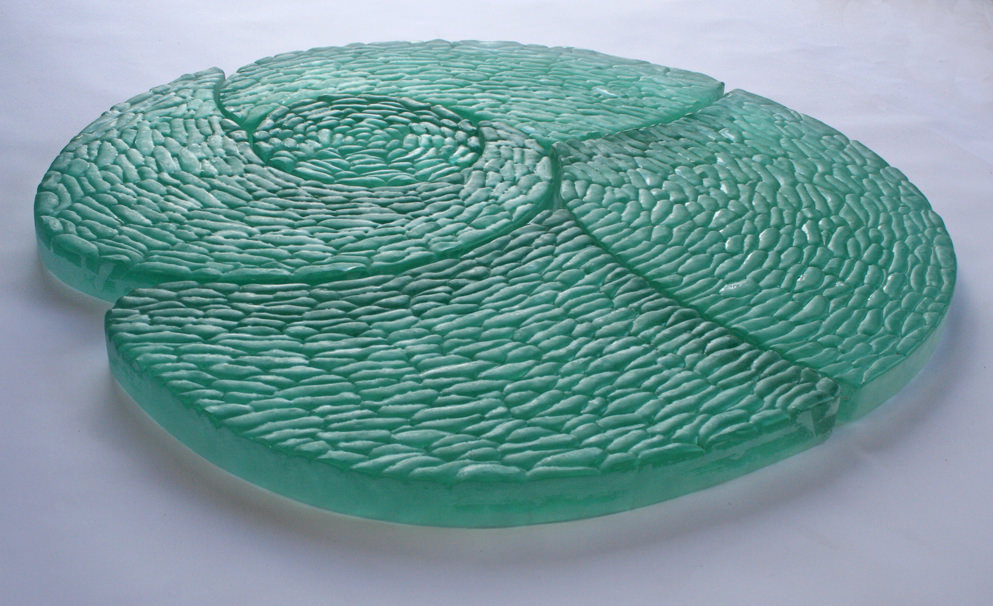
The Commons, downtown Kansas City :: 2012.
Whirlpool glass tiles after firing. We worked with an architectural glass company to develop this new kind of tile. The shapes are made from chunks of recycled glass that are arranged in a laminar pattern and then fused together in a mold.
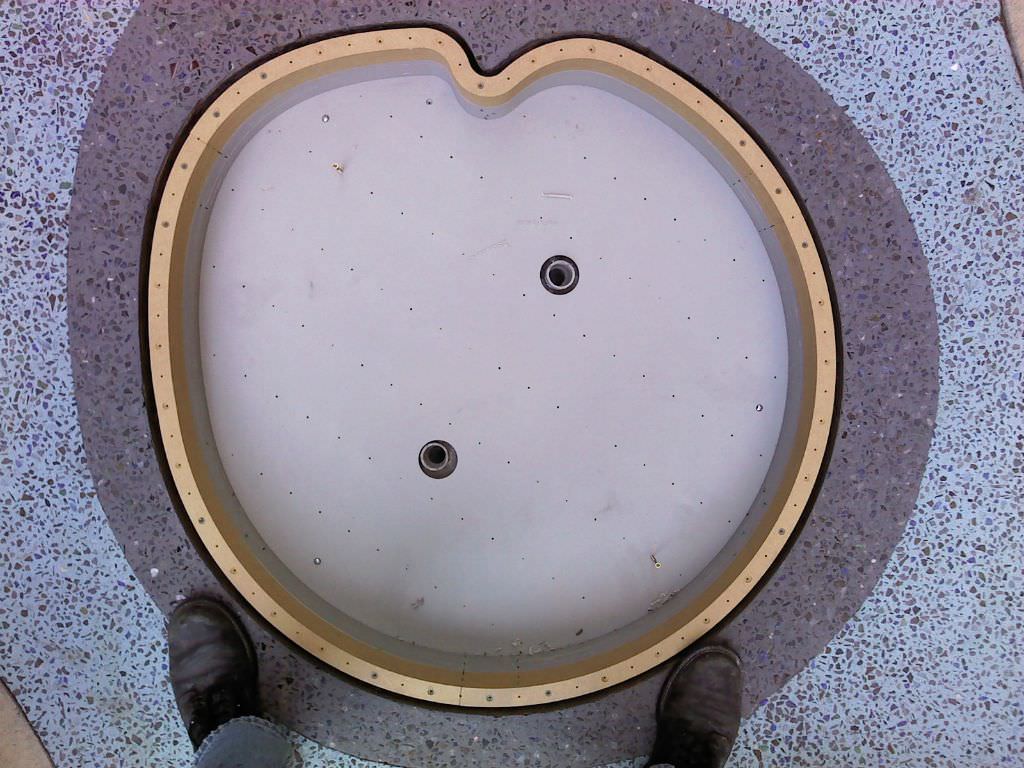
The Commons, downtown Kansas City :: 2012.
Fitting the pool unit on site. Here we were making sure that the base structure for the lighting assembly would fit comfortably and well into the concrete cavity.
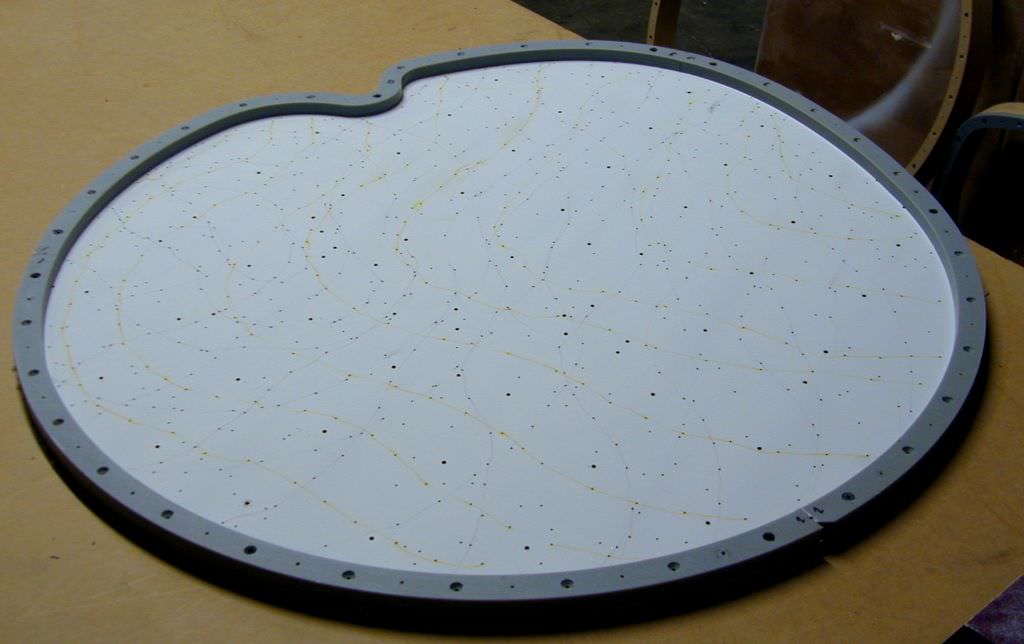
The Commons, downtown Kansas City :: 2012.
Pattern backer panel for inserting fiber optics. Installing all the fibers was a complex process in order to keep the forms of the ripple waves moving in unison across the glass tiles.
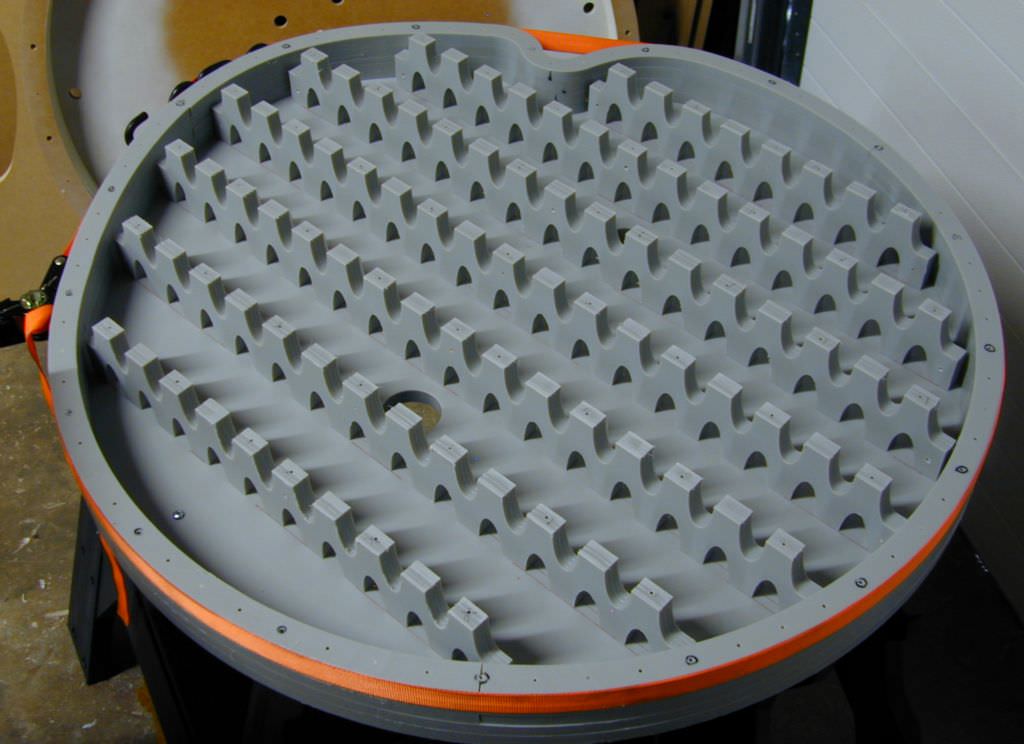
The Commons, downtown Kansas City :: 2012.
Spacer patterns for the pool unit assembly. These structures allowed space for the fiber optics to protrude out of the back of the tile assembly.
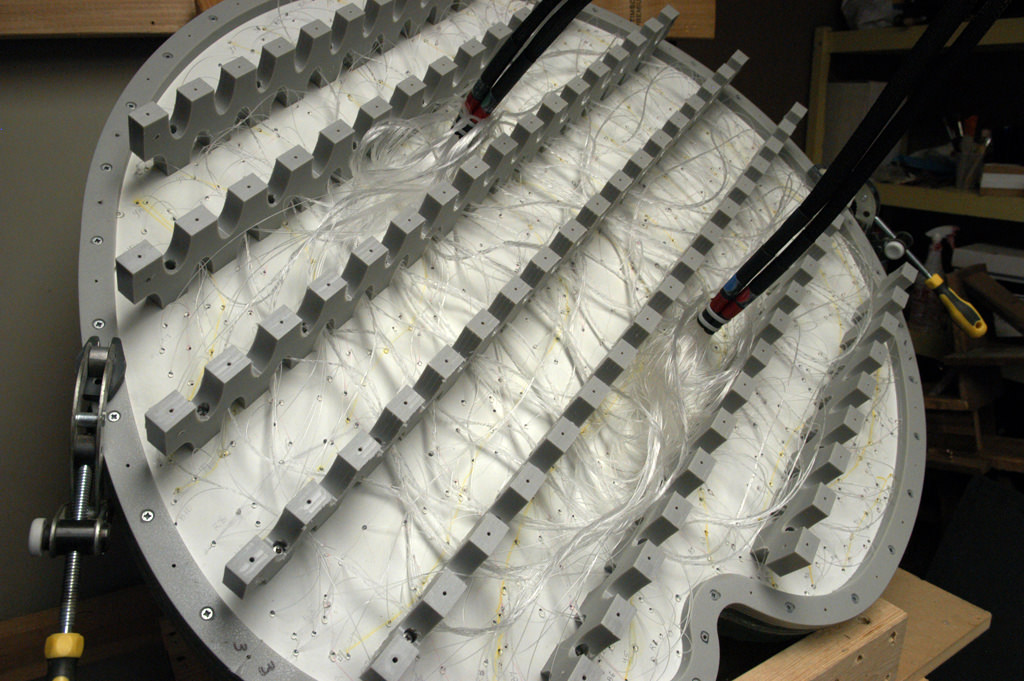
The Commons, downtown Kansas City :: 2012.
Detail of the fiber optic alignment on the back of the tile assemblies necessary to generate complex patterns from a simple rotating stencil on the light source.
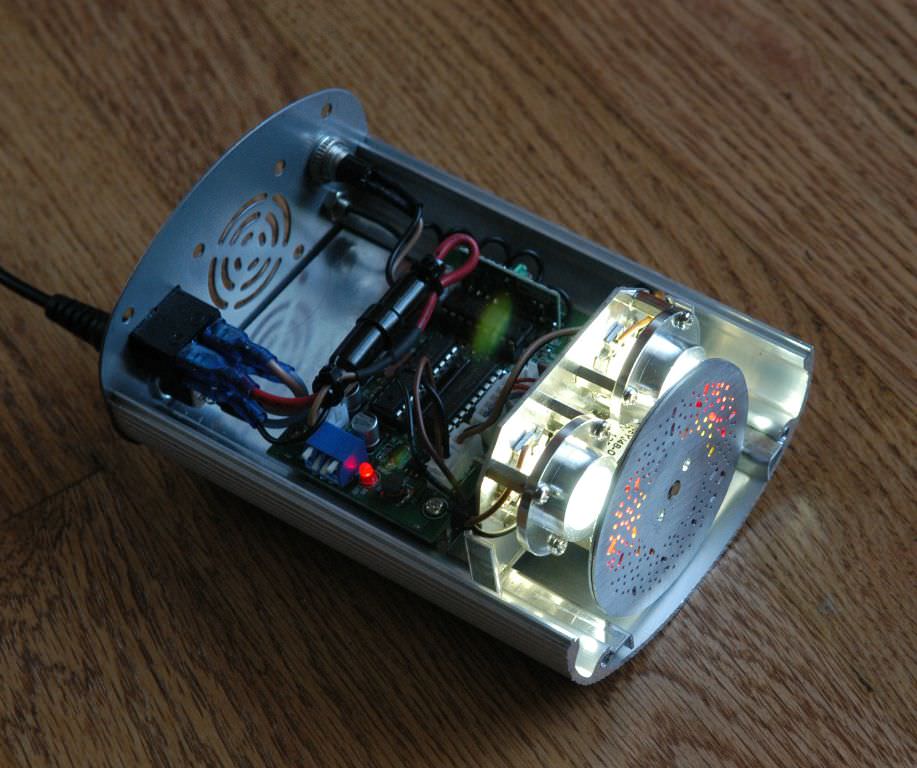
The Commons, downtown Kansas City :: 2012.
Illumination unit showing custom-cut stencil and rear-mounted light gels that generate colored light patterns. This unit is for the fire element. Two similar units were used for the more complex patterns in the pool unit.
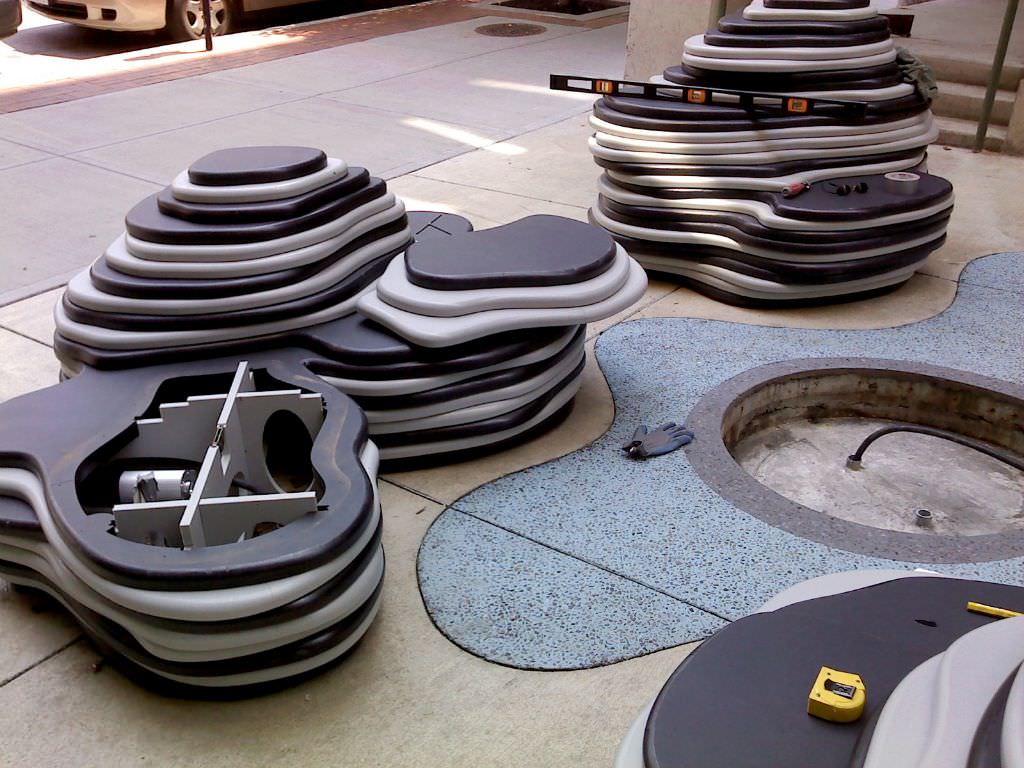
The Commons, downtown Kansas City :: 2012.
One of the illumination units installed inside one of the rock seating structures. All electrical connections for the lighting are above ground and accessible. Only the fiber optic strands pass through conduit embedded in the concrete.
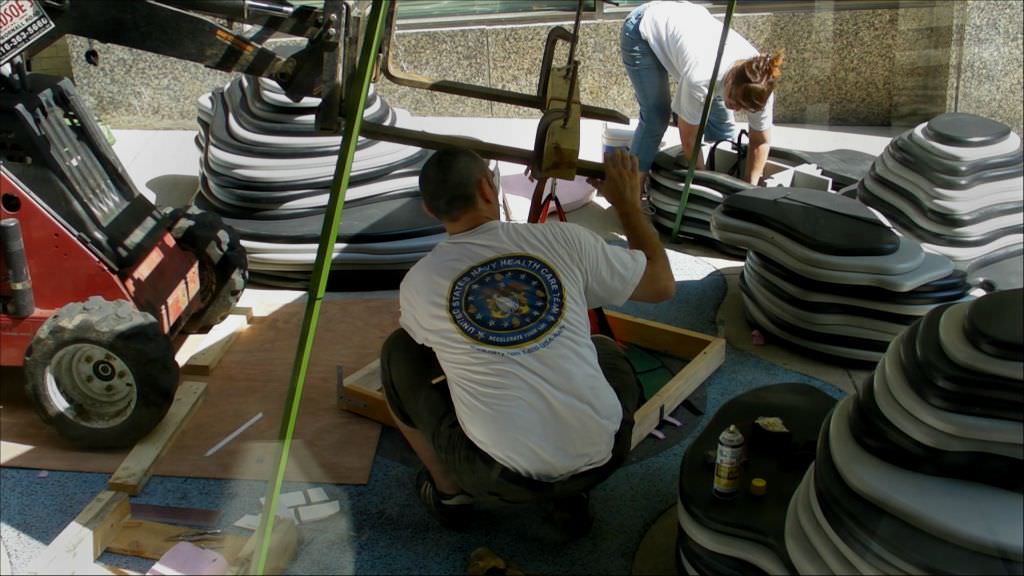
The Commons, downtown Kansas City :: 2012.
Installation of the larger embedded lighting unit on site. The assembled unit made up of HDPE structural components, fiber optics, glass tiles and polyurethane rubber holding everything in alignment weighed around 250 lbs. We needed a hydraulic front loader to lower it gently into place while feeding the fibers through the embedded conduit.
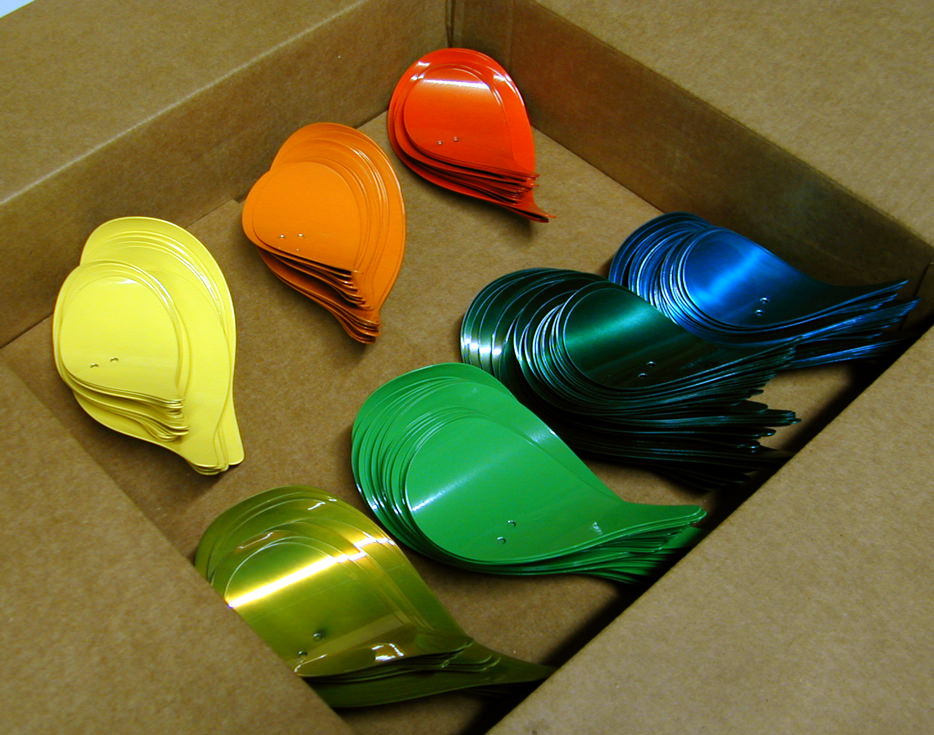
The Commons, downtown Kansas City :: 2012.
Powder-coated bird forms. These are the basic forms for the Ghost Bird sculpture. The shapes were cut from sheet aluminum, rolled, drilled, sanded, cleaned, masked and powder-coated.
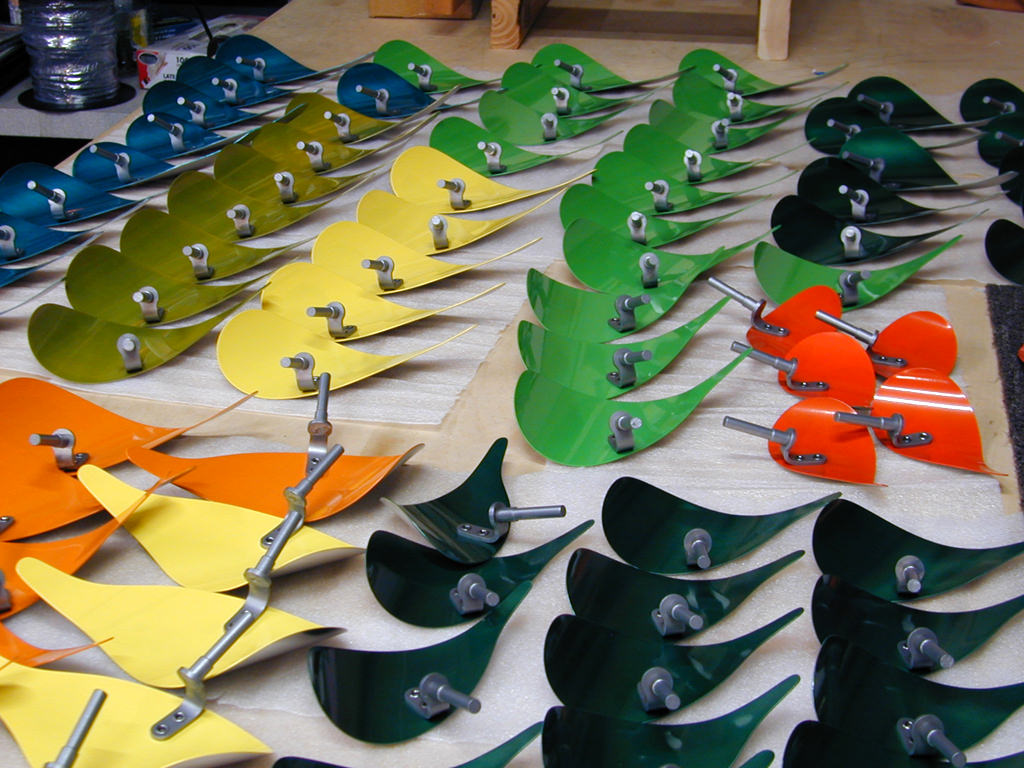
The Commons, downtown Kansas City :: 2012.
Bird forms with custom brackets and welded pivot shaft riveted on, ready for assembly onto the final panels.
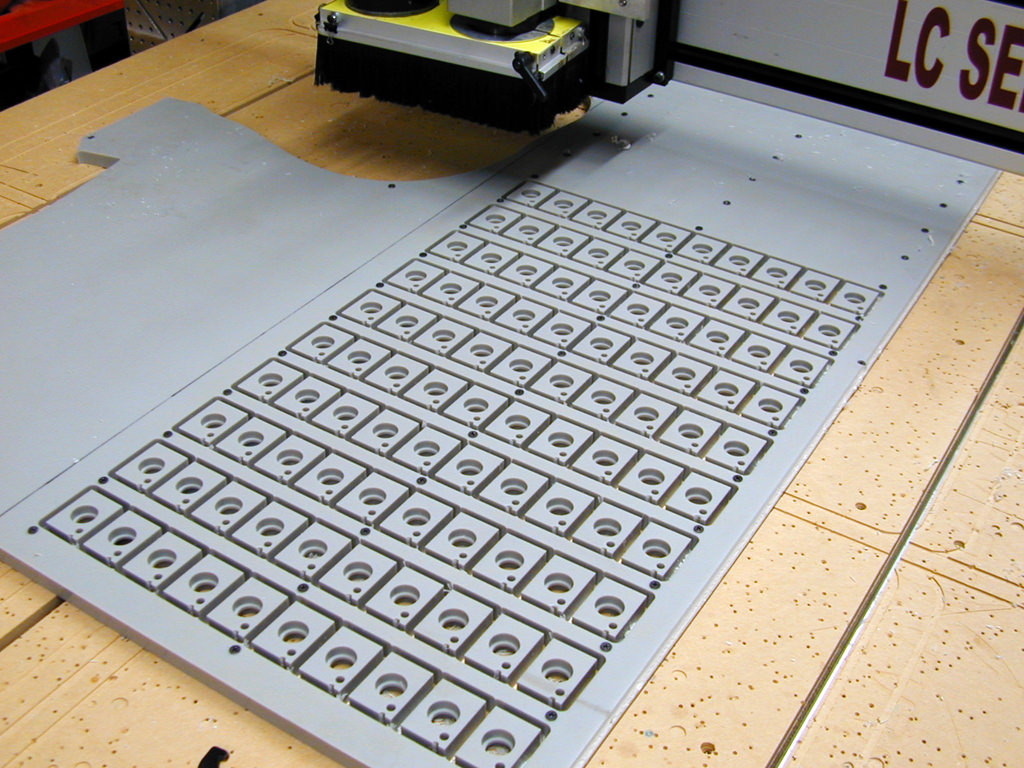
The Commons, downtown Kansas City :: 2012.
Cutting bearing blocks from recycled HDPE sheet material on the CNC router. Each block was designed to hold two skateboard bearings, one in front of the other, to give a stable and durable mechanism for the movement of the bird units back and forth in the wind. They also contain a hole for the led lighting cable to pass through.
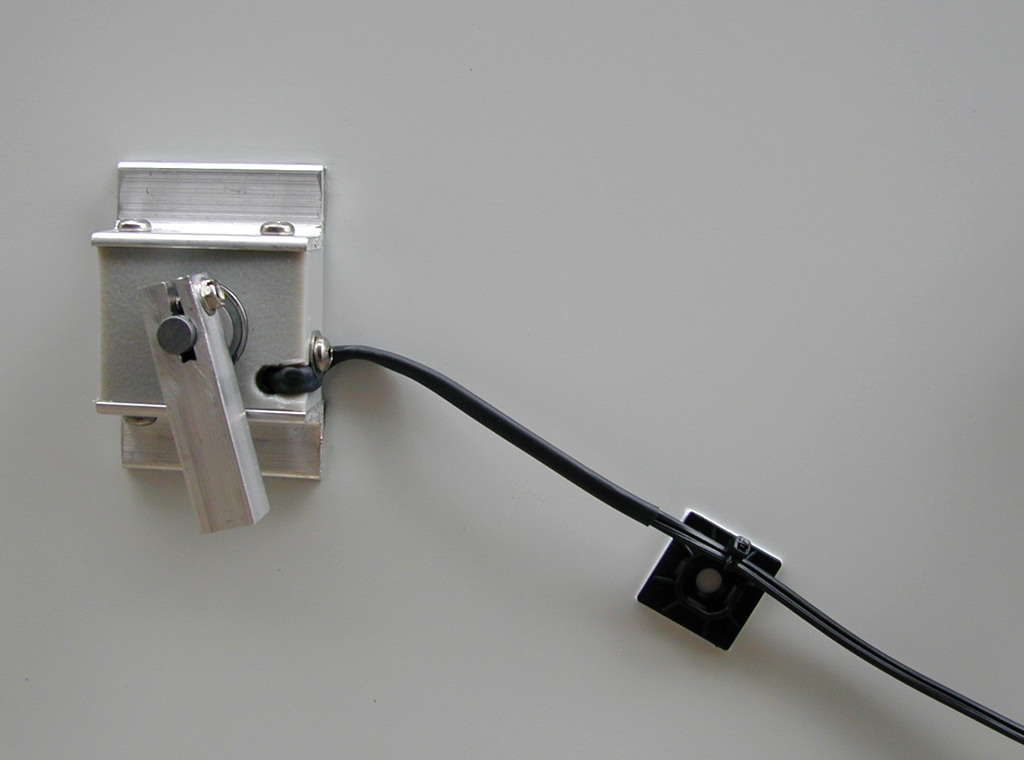
The Commons, downtown Kansas City :: 2012.
Back of a wall sculpture panel showing an assembled rocker mechanism and counterweight, and the wiring for the LED lighting on one bird unit. The cables had to be carefully routed and held in place so as not to interfere with the free movement of the bird units.
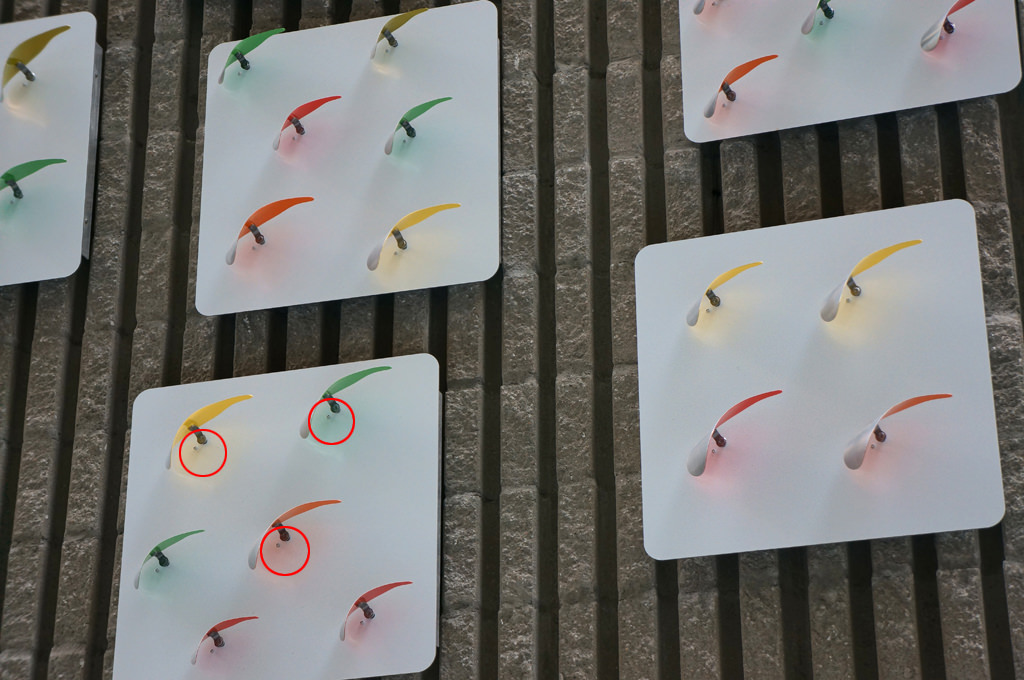
The Commons, downtown Kansas City :: 2012.
Front of some completed panels, showing small lengths of aluminum tubing protruding from the backer panel, each housing a single, warm-white led per bird unit. The tubing was cut at an angle to minimize glare for viewers in the alley below.
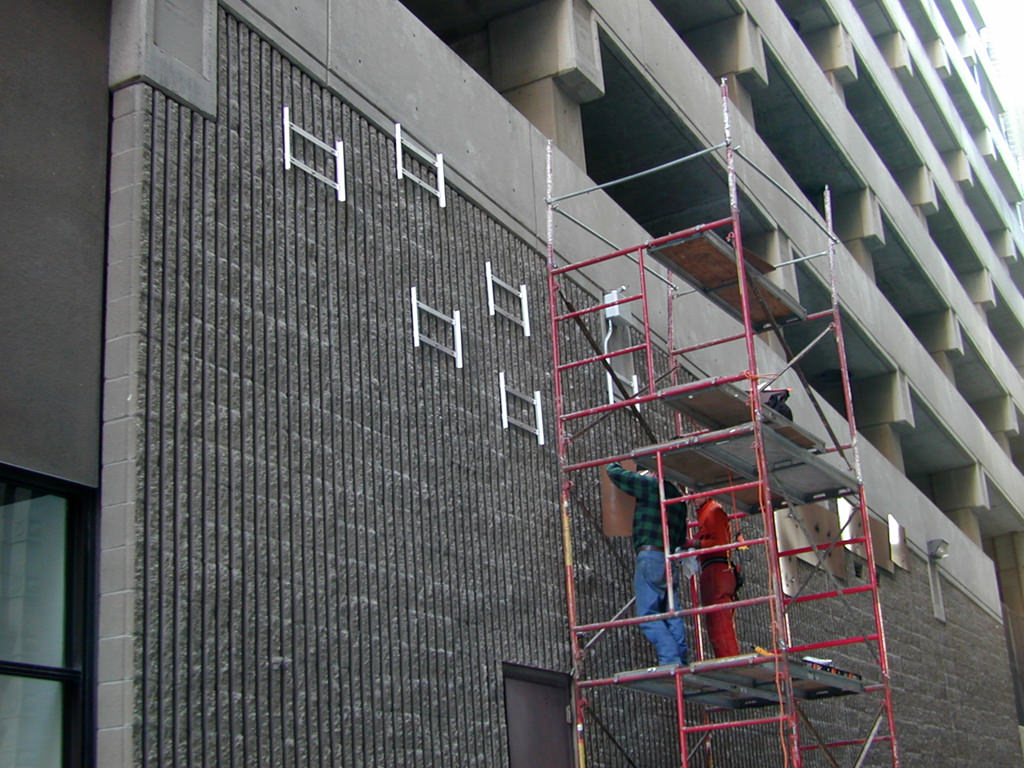
The Commons, downtown Kansas City :: 2012.
We made masonite templates to mark the position for each panel on the wall, and then used these to mount support frames onto which the panels would bolt.
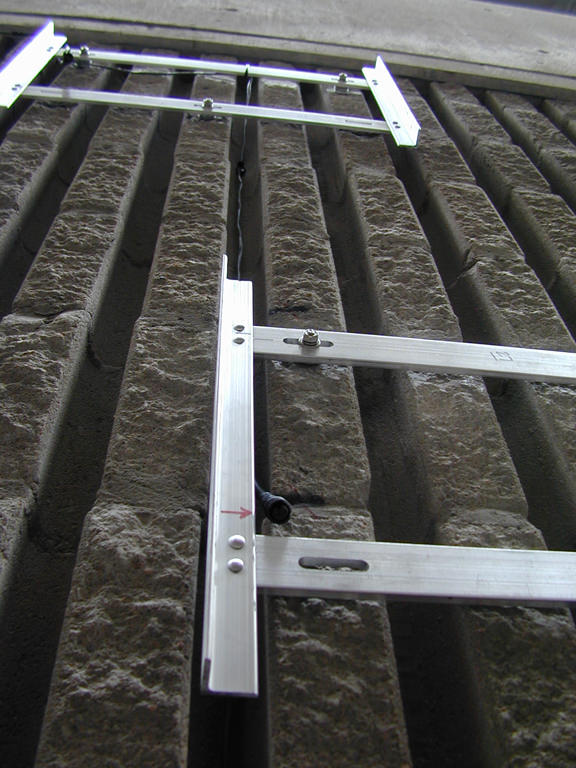
The Commons, downtown Kansas City :: 2012.
We used the grooves in the wall cladding to run electrical wiring for each panel, leaving a waterproof pigtail at the end of each run into which a panel would plug.
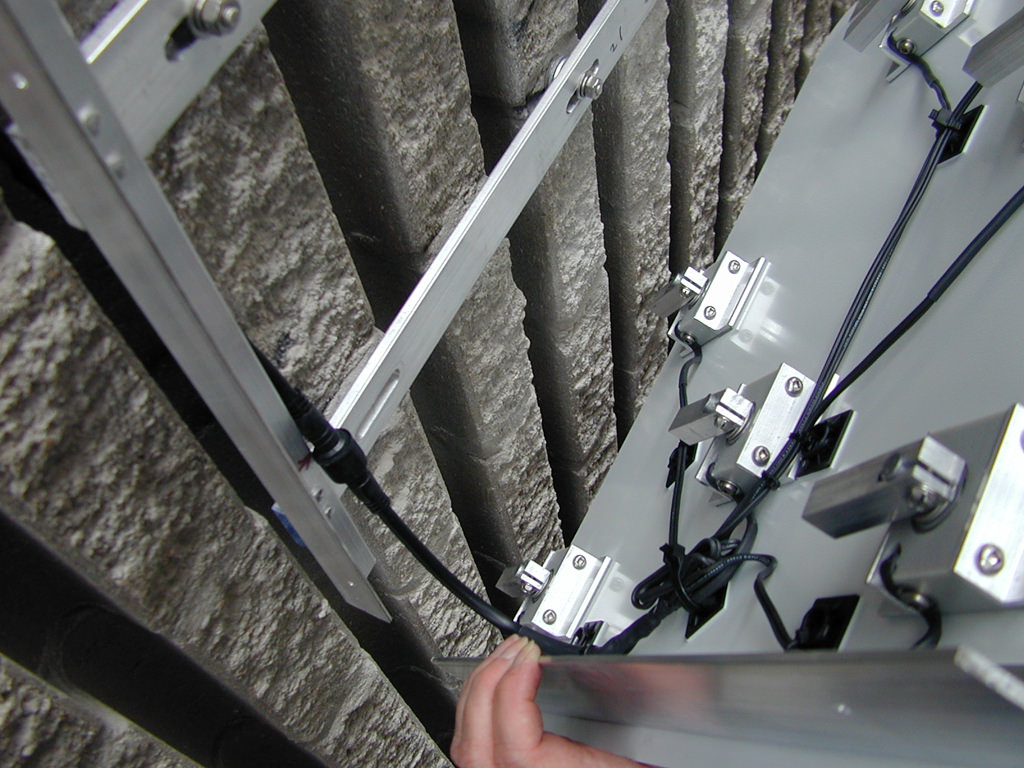
The Commons, downtown Kansas City :: 2012.
Connecting the panel electrics prior to final installation.
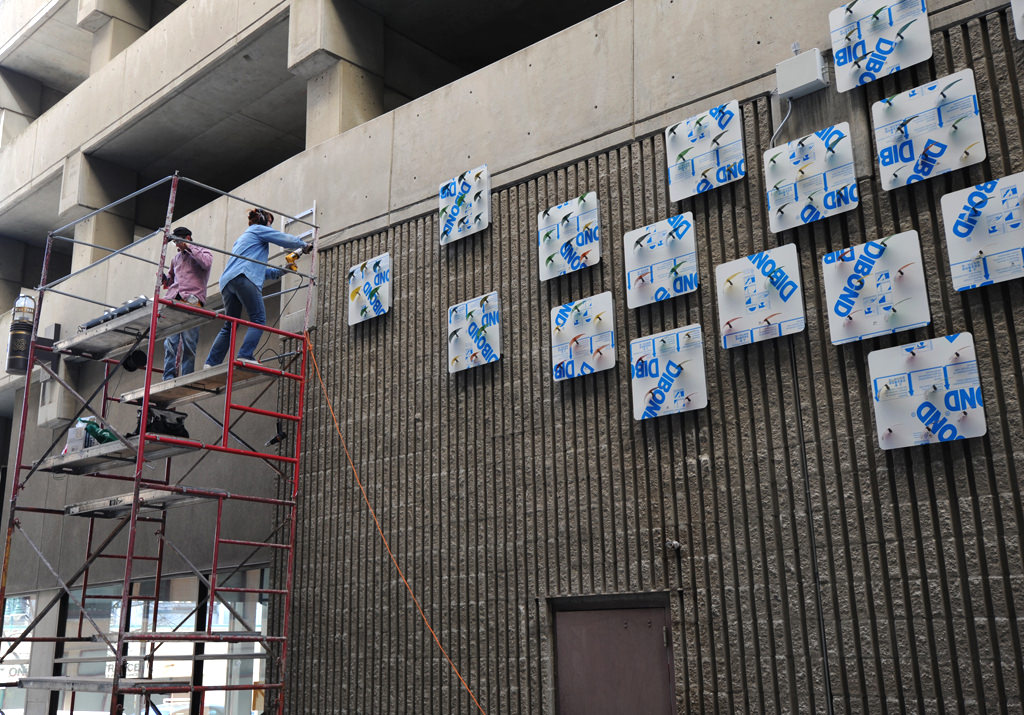
The Commons, downtown Kansas City :: 2012.
We were able to run close to 200 Ghost Bird LEDs from a single pre-existing light fixture (seen at upper right). The photo sensor that controls ambient lighting in the alley also switches on the led illumination for the Ghost Birds sculpture and the embedded pool and firepit lighting units.
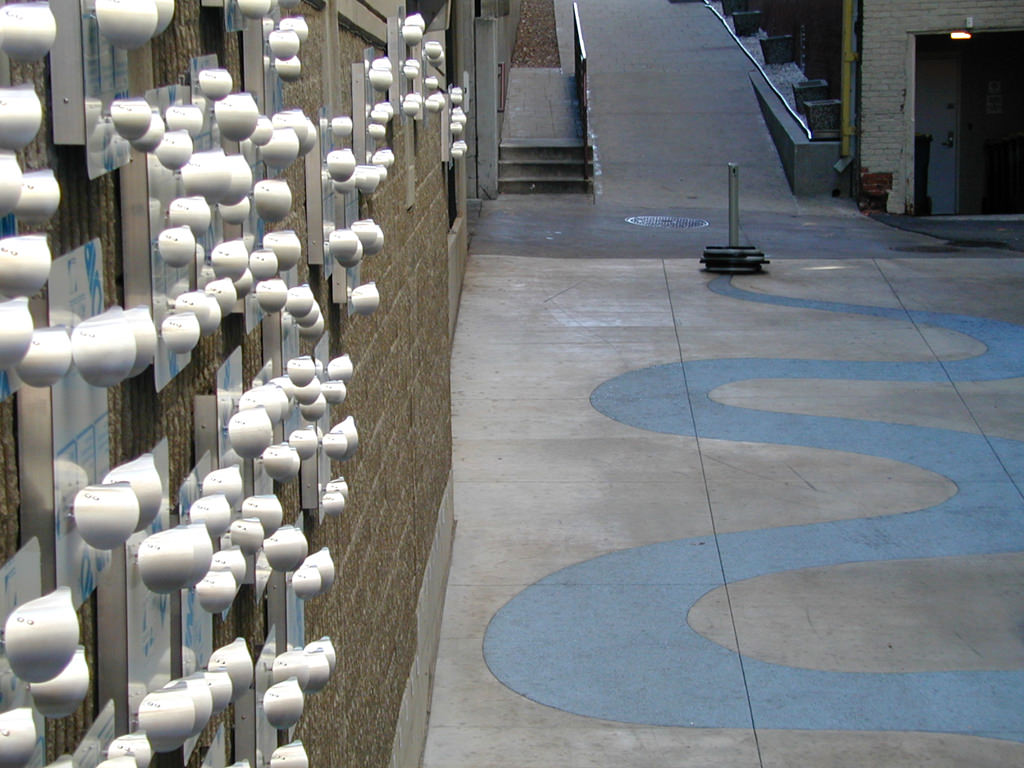
The Commons, downtown Kansas City :: 2012.
View across the completed sculpture from the scaffold, prior to removal of the protective sheet on each Dibond backer panel.
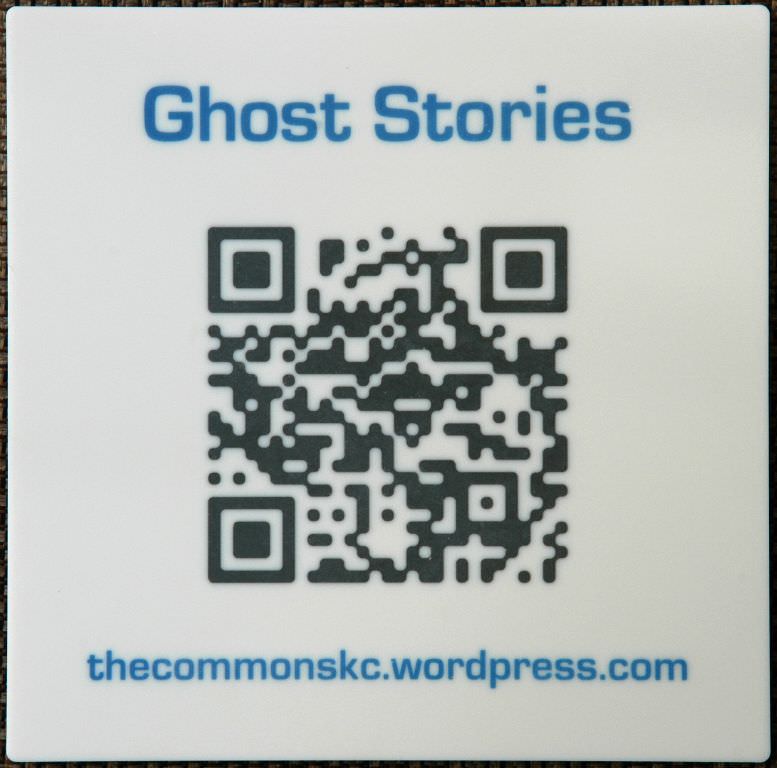
The Commons, downtown Kansas City :: 2012.
The QR tile linking visitors to The Commons website was made by routing the text and image into Corian, inlaying two colors of resin adhesive and then sanding the surface smooth.
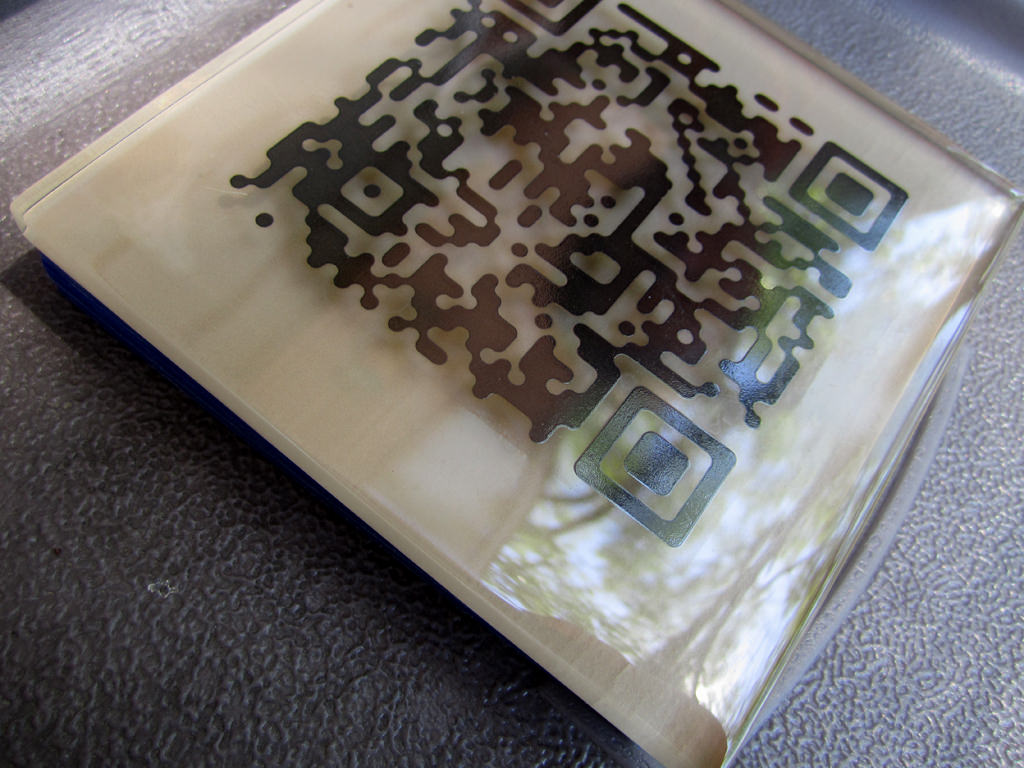
The Commons, downtown Kansas City :: 2012.
The series of story code QR tiles were made by firing digitally printed decals onto off-the-shelf freeze-tolerant glass tiles.